Abrasive Blast Nozzles
Abrasive Blast Nozzles for Blasting, Spraying and Peening
Abrasive blasting work, as one of the most important procedures in surface treatment, requires quality tools for an optimally constant operating and permanently stable performance properties. With our nozzles, these requirements can be well met at attractive costs. The wear resistance, which is ensured by boron-deponsed carvitation-resistant alloy (XCAB) or self-sintered silicon carbide (XSC) or self-sintered boron carbide (XSB) or hot-pressed boron carbide (HBC ), allows well-proven workable and economical results in practical uses.
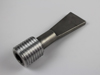
Boron-deposed Cavitation-resistant Alloy (XCAB) Blast Nozzles
XCAB is a combination of a cavitation-resistant alloy whose functional surfaces have been deposed with boron. This material combination is widely used in sandblast nozzle applications. With no difference in weight from Tungsten Carbide nozzles, XCAB nozzles provide higher toughness and serve as a very economical alternative.
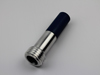
Silicon Carbide (XSC) Blast Nozzles
XSC is an innovative self-sintered Silicon Carbide (SiC) material. Based on a nano-level ultrafine SiC recipe, our XSC, which bears 20% higher hardness and toughness than conventional SiC material, provides at least 20% longer lifetime than existing SiC solutions at same costs.
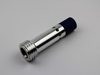
Self-sintered Boron Carbide (XSB) Blast Nozzles
XSB is a cutting-edge self-sintered Boron Carbide (B4C) material, which is primarily used in the manufacturing of nozzle liners. The unique production process drastically reduces manufacturing costs and make possible the manufacturing of even the most complex shapes. With 30% higher toughness and almost same lifetime compared to hot-pressed boron carbide with most of abrasives, XSB serves as the most economical solution and one-stop material for high pressure blasting applications using all kinds and sizes of hard abrasive materials.
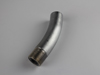
Hot-pressed Boron Carbide Nozzles (XHB)Blast Nozzles
Hot-pressed boron carbide (XHB), as one of the hardest materials known, offers excellent chemical and wear resistance for various demanding applications. Therefore, our XHB nozzles are used for those most wearing abrasives such as alumina and silicon carbide for efficiency-optimized reasons.
The following is a lifetime contrast of our nozzles against main abrasives:
Mat'l of Nozzle | Steel Shot | Quartz Sand | Brown Alumina |
Alumina (Al2O3) | 20-40 Hours | 10-30 Hours | 1-4 Hours |
Tungste Carbide (WC) | 500-800 Hours | 300-400 Hours | 20-40 Hours |
XCAB | 500-800 Hours | 300-400 Hours | 10-30 Hours |
XSC (SSiC) | 700-1700 Hours | 700-1000 Hours | 350-700 Hours |
XSB (SB4C) | 1900-2300 Hours | 950-1400 Hours | 450-950 Hours |
XHB (HB4C) | 2000-2500 Hours | 1000-1500 Hourse | 500-1000 Hours |